
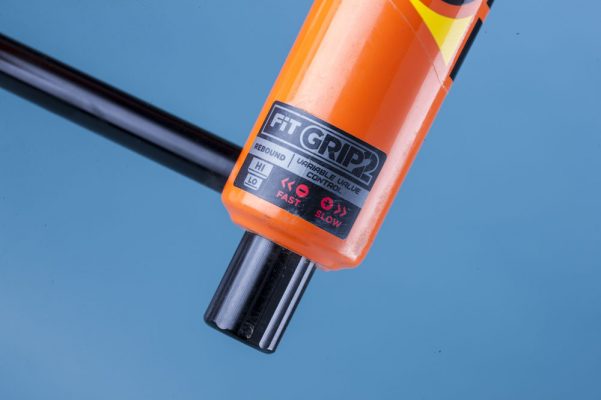
Namtvedt, president of FloaTEC, thinks that the optimized subsea solution will involve new technologies such as subsea processing and boosting, ESPs, all-electric systems to enable further step-outs, and compact tree designs. Olivier Saincry, Doris Engineering subsea systems manager, foresees the optimization of subsea system installations “residing in the use of autonomous equipment, maintenance work without the use of surface support vessels, and a number of topside processes being done subsea, limiting the number of links between the seabed and surface.”Įric H. “Daisy-chained pipeline loop (like Canyon Express) or field hub (like Independence) approaches to field development will be the norm, since most oil companies will have to form consortiums to share in the infrastructure costs.”įinally, oil and gas companies are accepting the notion that subsea metering, boosting, and separation are smart and economical means to address both infrastructure-lean areas of the world and longer offset distances, Skeels contends: “The bigger picture is getting the overall recovery rates of subsea fields up to be on par with conventional platform completions for the same cost.” Smart subsea field architects will add plug-in bases in the field pipelines that can accommodate the later installation of more infrastructure when it’s needed, without disturbing what was initially installed. Subsea production facilities can be added later in a modular plug-and-play scenario to deal with production plateaus or changes in well count. “This modular approach also lends itself to easier installation and a pay-as-you-go schedule. “Clustered wells leading to manifolds connected by umbilical flying leads and jumper connections allow for smaller modular components that can be set on the seafloor side-by-side and then connected up,” he says. The days when all of the equipment and trees mounted on one-of-a-kind giant templates with integrated and form-fitting piping and connections are fading into the past, claims Brian Skeels, emerging technology manager, FMC Technologies. Other hallmarks of tomorrow’s deepwater production facilities will be increased automation, more modularization, improved size/weight ratios, longer tiebacks, and expanded use of subsea processing. Much of the design changes will entail borrowing the basic concepts in use today and reconfiguring them in new ways. The flapper also closes quickly keeping cuttings out of the drill string preventing plugging of the bit.Īll Float Sub IBOPs are extensively tested in our facilities to ensure the highest quality and that the product will perform to specifications when used in the field.As the offshore oil and natural gas industry continues its march into deepwater frontiers, the facilities that will be the mainstays of that push, subsea installations and floating production facilities, will take on a distinctively different look. The flapper float assembly provides a completely unrestricted bore through the valve and is designed for highly abrasive fluids.
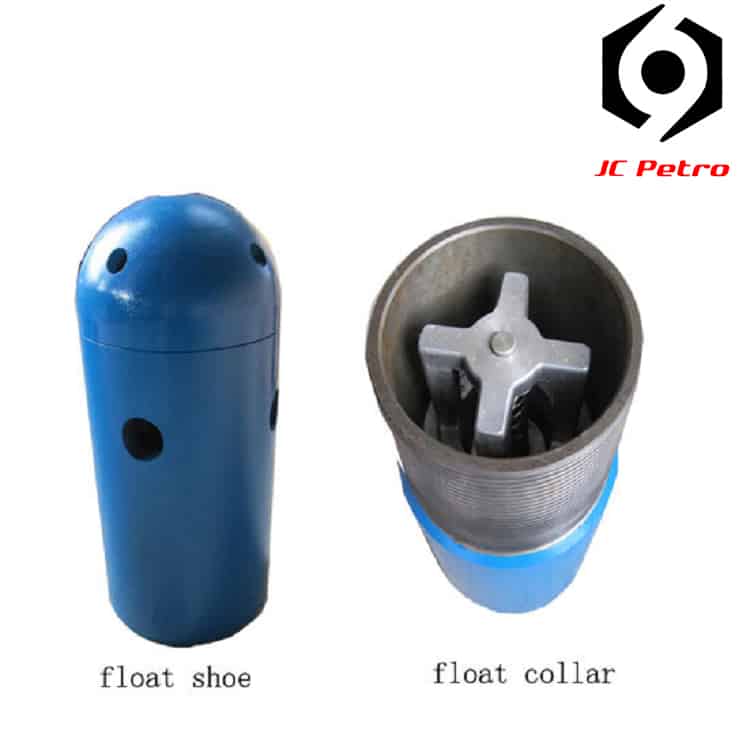
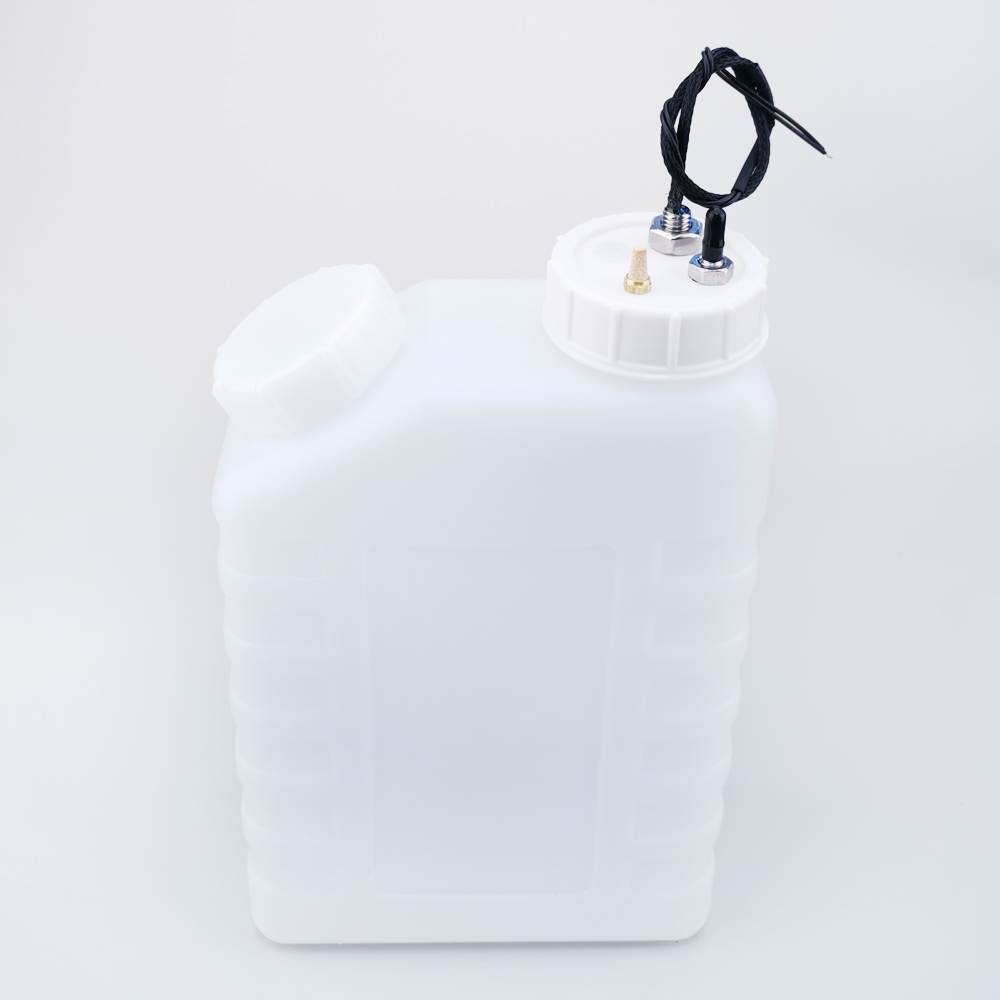
The plunger (dart) float assembly offers positive and instant shut-off, assuring continuous control of fluid flow during drilling. Float Sub IBOPs are available in 5000 or 7500 PSI.

The Float Sub IBOPs are available in one or two piece body construction and are supplied with either API or proprietary connections. Featuresĭ‑Valves manufactures the Float Sub IBOP body and sub from chromoly steel and uses third party, industry approved, plunger (dart) and flapper float assemblies. It also allows for downward fluid circulation within the drill string. The Float Sub IBOP is used to control back flow from high pressure formations through the drill string back to the surface when joints are added.
